3d print and test

The development of a mesoscale structural model, rather than a continuum model, allows for additive manufacturing of the resulting structure. With suitable manipulation of the bone adaptation algorithm, 3D printing in materials including a wide range of polymers and metals, permits the manufacture of frangible bone simulants for use in experimental testing, as well as the potential design and manufacture of bioresorbable scaffolds and orthopaedic implants, sympathetic to the remaining skeletal structural architecture.
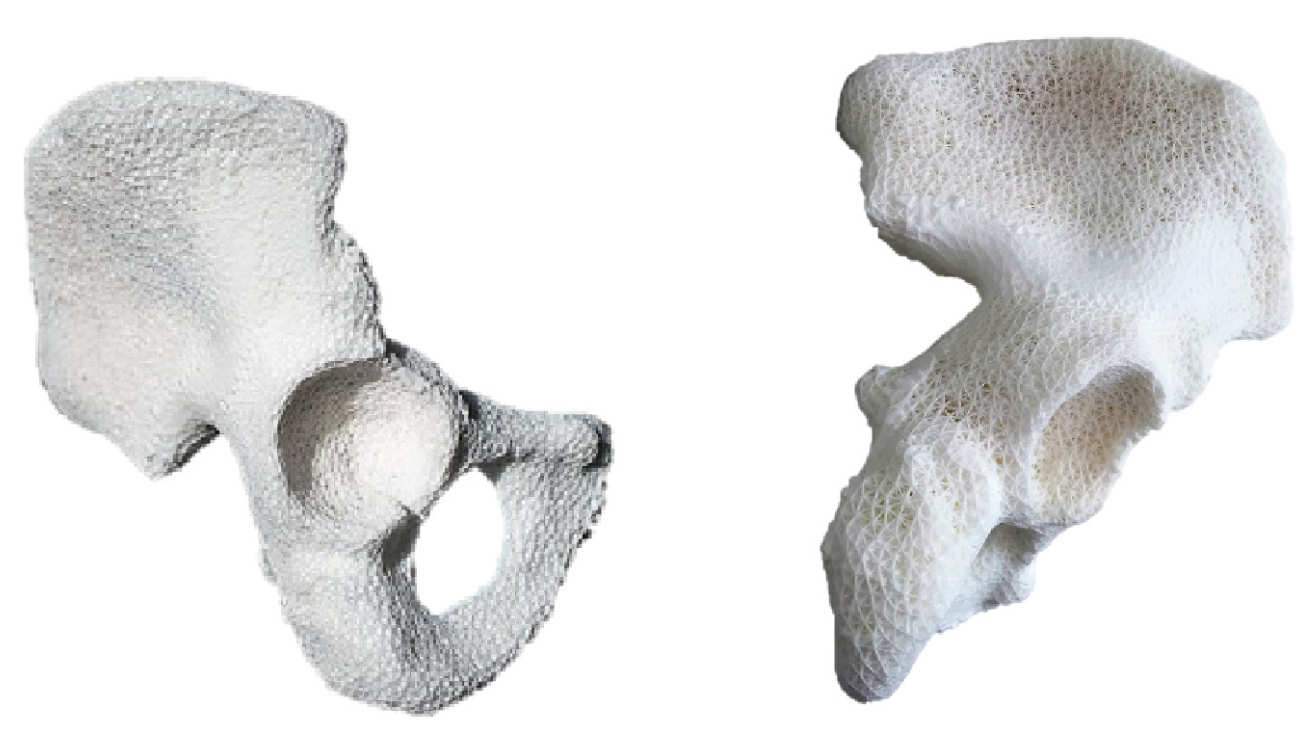
A preliminary study was funded by the Defense Science Technology Laboratory (DSTL), in cooperation with Imperial College London, which constitutes a Phase 1 manufacture of a human lower limb frangible surrogate for use in ballistic, impact and blast testing, indicating realistic injury patterns. It was designed as a proof of concept for the production of such surrogates using additive manufacturing based on computationally derived bone structures.

As a result, frangible surrogates representing individual pelvis, femurs, tibia/fibula systems with membrane and ligaments were designed based on the mesoscale models. A picture of a half proximal femur print is given in Figure 1. Figure 2 shows the print of the right pelvis trabeacular bone. Nylon material tests were conducted prior to the surrogate manufacture to inform the surrogate design. A full lower limb surrogate including knee, knee ligaments, and a representation of soft tissue in the thigh and the shank was also designed and manufactured (Figure 3).
Researchers
Contact us
Dr Andrew Phillips
Imperial College London
Structural Biomechanics
Skempton Building
South Kensington Campus
London SW7 2AZ, UK
Creative Commons license
This work by Imperial College London, Structural Biomechanics is licensed under a Creative Commons Attribution-NonCommercial-ShareAlike 4.0 International License.