Our state-of-the-art multidisciplinary facilities help provide researchers and students the best collaborative and supported environment in which to learn and conduct novel and world leading research
Department of Bioengineering offers world-class facilities for micro-and nanofabrication. These interdisciplinary facilities are dedicated to developing micro and nano-scale technologies, including but not limited to lab-on-chip and organ-on-chip technologies.
These facilities are managed by a group of highly experienced PhD-leveled technicians, providing an efficient and effective means of delivering key technologies and ensuring the maintenance of a skills repository, which is essential in delivering our leading international activities.
The facilities are open to all members of the department plus those from the wider Imperial College community and beyond.
More information for Imperial staff can be found on the facilities' wiki pages.
Micro and Nanofabrication Facilities
CRUK Microfabrication Facility
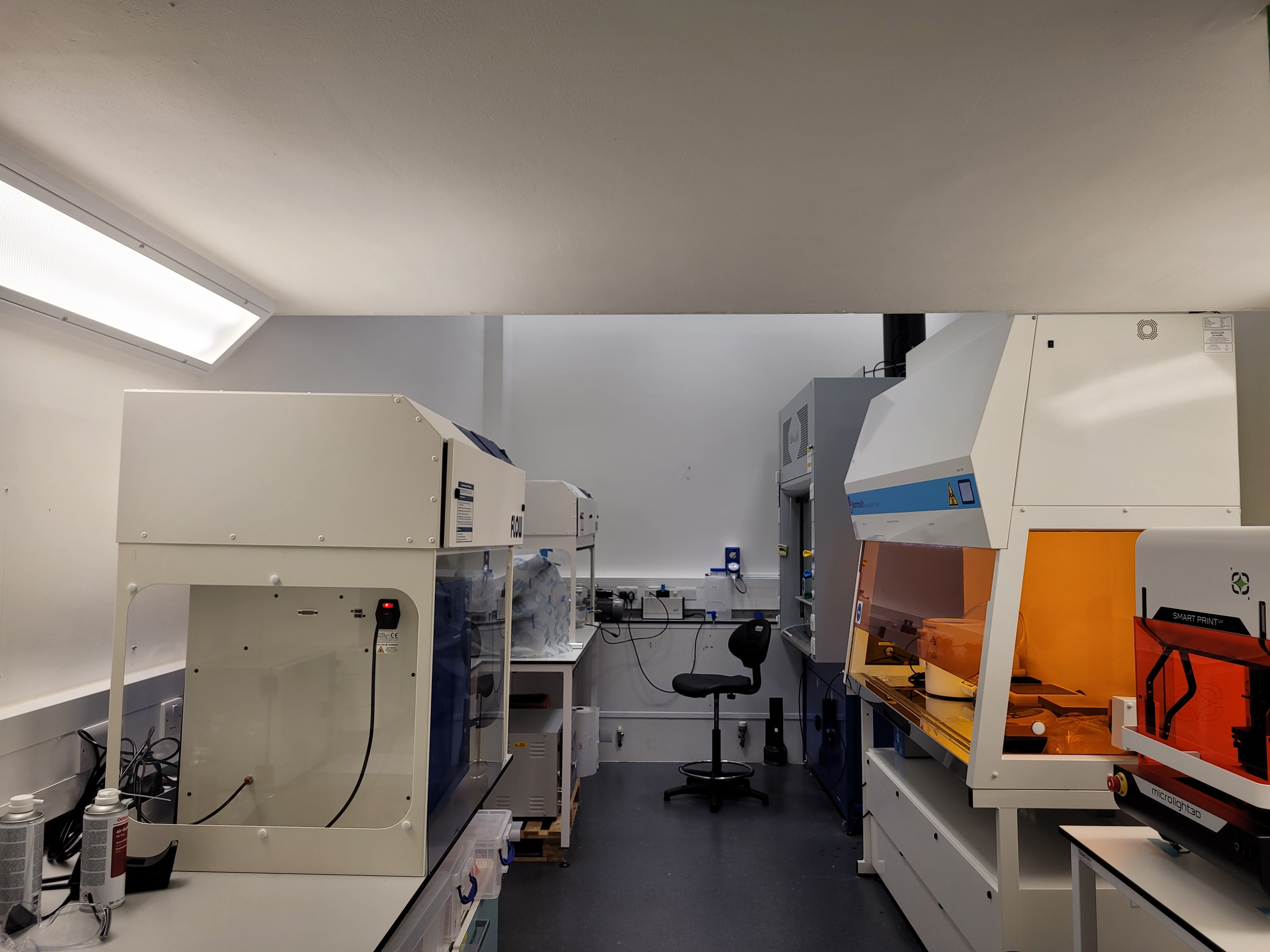
This facility offers a full range of services for prototyping SU-8 and PDMS micro-devices, including a clean lab. The user-friendly setup of the facility enables researchers from different disciplines to perform SU-8 photolithography and PDMS micro-chip casting with a high resolution of 5 µm and a broad thickness range from 5 µm to 250 µm. The training process is quick, and you can use the facility after 2 days of training.
For more information about training and access to the facility, please check the "New User" page on Wiki.
Imaging essential information, access, contacts
CRUK Microfabrication Core Facility - South Kensington
SU-8 Station
The SU-8 station with a state-of-art laminar hood equipped with "Hotplate EMS 1000-3", "Spin Coater WS-650MZ Modular", and "Hotplate Torrey Pines" can provide:
- Fabrication resolution of 5 µm
- 3” and 4” wafer coating
- 5 µm to 250 µm SU-8 coating
- Four programmable heat ramp steps
Mask Aligner
The UV-KUB 3 is a new generation of compact mask aligner which can provide:
- Resolution of 1 µm
- The alignment accuracy of 1 µm
- Hard (physical) or soft (proximity) contact processes
- 100 numbers of programmable cycles
Smart Print UV
Smart Print UV is a multi-purpose maskless photolithography tool based on a UV light engine technology with excellent features, including:
- 2D printing with a high resolution of 1.5 µm
- Printing complicated geometries
- Printing on a wide range of SU-8 thicknesses
- Printing on different substratesUser-friendly software interface
- Alignment of several layers
CRUK Microfabrication Facility
Bionanofabrication Clean Room Core Facility - White City
The Oxford Instruments Plasma Cluster is composed of three chambers and a handling unit. Two PlasmaPro 100 Cobra chambers are set up as ICP deposition and ICP etching and on Flexal ALD system. Wafers can be carried from one chamber to another without exposing to air via the central handling unit.
Chamber 1: Flexal II ALD System
The Flexal II ALD chamber is dedicated to plasma and thermal ALD deposition.
This unit is equipped with a manifold that can host up to 3 precursors as well as water vapor and hydrogen gas.
This chamber allows for the deposition of extremely conformal film with an atomic precision.
Current materials available include: Al2O3, TiO2, TiN and HfO.
Chamber 2: PlasmaPro 100 Cobra ICP Etching
The ICP Etching chamber has been designed to offer versatile etching capabilities adapted for the fabrication of complex structures in silicon and other materials. The local gaspod offers the possibility of fast switching Bosch process for high aspect ratio structures. The system is equipped for silicon etching, glass etching, chlorine etching, teflon deposition and more.
Chamber 3: PlasmaPro 100 Cobra ICP Deposition
The ICP deposition chamber allows for fast deposition of thick layer of silicon oxide and silicon nitride using silane precursors. It also allows for controlled process monitoring using in-situ spectrometric reading.