Our aim is to employ an integrated approach comprising experimental, analytical and numerical techniques. Here are some examples of our research activities:
Projects
- Experimental and numerical investigation of soft impact loading on aircraft materials
- Blast performance of laminated glass structures
- Blast performance of composite structures
- Transparent materials for aircraft
- Composite materials for wind energy applications
- Fracture and fatigue studies on transparent polymers for aircraft cockpit applications
- Constitutive material properties in static and dynamic conditions
- Modelling of solid-state lithium batteries
- Li-ion battery thermal runaway modelling
Jie Zhou, Iman Mohagheghian, Gordon Williams, John Dear, Maria Charalambides
To fully understand the mechanical behaviors of the bird and target material during the impact, an appropriate “bird” substitute is essential in order to achieve consistent and repeatable impact results each time. Hence, the selection of the bird simulant materials was the first objective in the study and the details of choosing the bird surrogate materials were described in the literature. Subsequently, appropriate mechanical tests were conducted to investigate the mechanical behaviors of the bird substitute materials, starting from the low rate quasi-static test (0.25 min-1) to the high rate of 33000 min-1. Then, gas gun tests were performed to match the rate that the aircraft experience from the bird strike during the take-off or landing periods. Hence, the main objectives of the project are summarized below:
I. Bird substitute material (soft materials) selection
II. Quasi-static compression test of the selected soft materials (0.25 min-1 – 25 min-1)
III. Intermediate rate compression test of the soft materials (1 ms-1 – 8 ms-1 or 4,000 min-1 – 35,000 min-1)
IV. Impact performance of the compliant target (aluminium) using the soft materials at high velocity (100 ms-1 – 200 ms-1 or 120,000 min-1 – 240,000 min-1)
V. Impact performance of laminated glass using the soft materials at high velocity (100 ms-1 – 200 ms-1 or 120,000 min-1 – 240,000 min-1)


Mohammad Samieian, Paul Hooper, Bamber Blackman, John Dear
The propagation of a blast wave from the point of explosion can result in the failure of glass windows. Laminated windows are usually employed for protection in such a scenario. In protective design the following factors are important:
- Laminated glass pane must be able to absorb the pressure pulse via deformation.
- The frame and its fixing must survive.
- The pane must not detach from the frame.
The aims of the research are to use experimental and modelling techniques to have a better understanding of how laminated glass panels behave under blast loading. This would enable improved design tools and a more accurate prediction of failure in such panels.
We do experiments in the laboratory at high rates (up to 20 m/s) on a servo hydraulic test machine and also full scale blast tests. As an example, results from a blast test can be monitored using digital image correlation (DIC), as shown in figure 1. Silicone joints can also be tested in the laboratory (Figure 2).


Emily Rolfe, Hari Arora, Paul A. Hooper, John P. Dear
Composite structures employed in the naval sector experience large dynamic loads such as wave slamming, impact loading and blast loading. Due to the brittle nature of composites, unnecessarily high safety margins are used to ensure they can withstand these loads, counteracting the benefits of the composite materials.
This research uses experimental and finite element modelling techniques to further the understanding of composite behavior under high strain-rate blast loading. This will result in improved design and predictive tools.
Laboratory experiments are carried out using servo hydraulic test machines to achieve high rates (up to 20 m/s) and gas guns to simulate blast loading. Full-scale blast experiments are carried out at an external facility. Digital image correlation (DIC) is used to capture full-field displacement data of the composites during experiments.
Figure 1 shows the displacement of the central horizontal section of a composite sandwich panel during blast loading, this was generated from DIC data. Figure 2 shows a slow motion replay of a blast experiment.
Slow motion replay of a blast experiment on two composite sandwich panels
Iman Mohagheghian, Yi Wang, Jun Liu, Anthony J Kinloch, Maria N Charalambides, John P Dear
Modern aircraft windshields consist of several layers of strengthened glass and polymer interlayers. The purpose of this project is to understand the effect of different design parameters including the order of layers, the types of glass and polymer and the thickness of each layer on the performance of the laminated glass under different loading condition: quasi static loading, low and high velocity impact. Both experimental and numerical (Figure 2) approaches have been used. This study helps us to design a lightweight impact resistant glazing for aircraft windshield.
Numerical techniques to simulate soft body impact on laminated glass windows
Cihan Kaboglu, Soraia Pimenta, Iman Mohagheghian and John Dear
The research aim is to understand the effects of different core materials on the mechanical behaviour of sandwich composite structures and the effects of various configurations on the mechanical behaviour of fibre metal laminates. The study focuses on the failure modes of sandwich composite structures and fibre metal laminates under three-point and four-point bend, low velocity drop weight impact and high velocity impact tests, observed with digital image correlation.
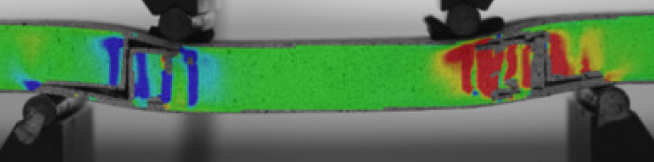
Sze Ki Ng, Bamber Blackman, John Dear
This project investigates the toughness and damage tolerance of transparent polymers as used in the aircraft industry for cockpit canopies. Such materials will experience a combination of continuous and alternating stresses during their service life, and due to the methods of attaching them to the rest of the structure, will be subjected to stress concentrations at attachment points.
This project will consider the quasi-static toughness, and fatigue of the polymer used, which is a bi-axially oriented PMMA. Fracture mechanics and damage mechanics methods will be employed to understand the in-service behaviour and predict performance.
The fracture mechanics compact tension specimen shown in figure 1 can be loaded in fatigue at a predefined frequency. This is to simulate repeated pressurised cycles in a cockpit application. In such a test, the rate of crack growth per cycle, is measured as a function of applied ΔK as shown in figure 2.
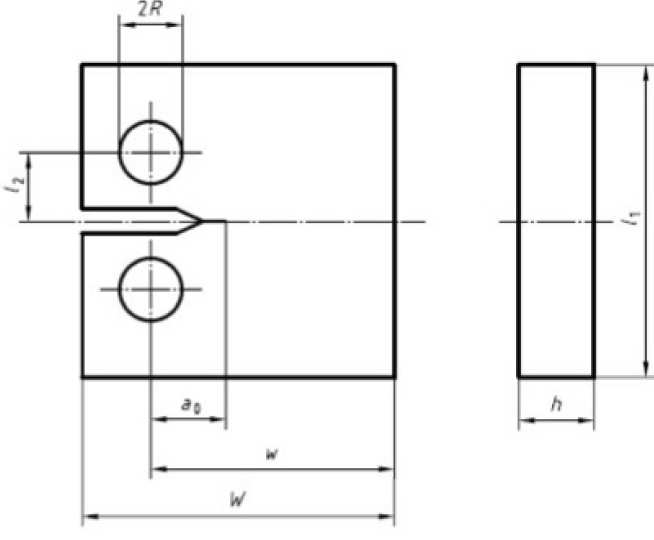

Alexander Sancho, Paul Hooper, Catrin Davies, John Dear
In order to predict the behaviour of a material numerical models are developed. These models are based on the actual response of the material, and therefore, they have to be calibrated through diverse experiments. As an example, Figure 1 shows the strain evolution of a specimen through a tensile test obtained using digital image correlation (DIC).
Once calibrated, the equations of these models can be introduced into simulation tools such as finite element (FE) codes to analyse stress, strain, damage and other properties of real components under various conditions, reducing considerably the requirement of experimental work. In Figure 2 a FE model has been created to simulate a tensile test similar to that presented in Figure 1.
This research is focused on the use of continuum damage mechanics models to predict the damage accumulation in a material as well as its elasto-plastic behaviour when it is subjected to extreme conditions of temperature and strain-rate. Non-conventional experiments are run and their results used to extend the validity of numerical models to these conditions.
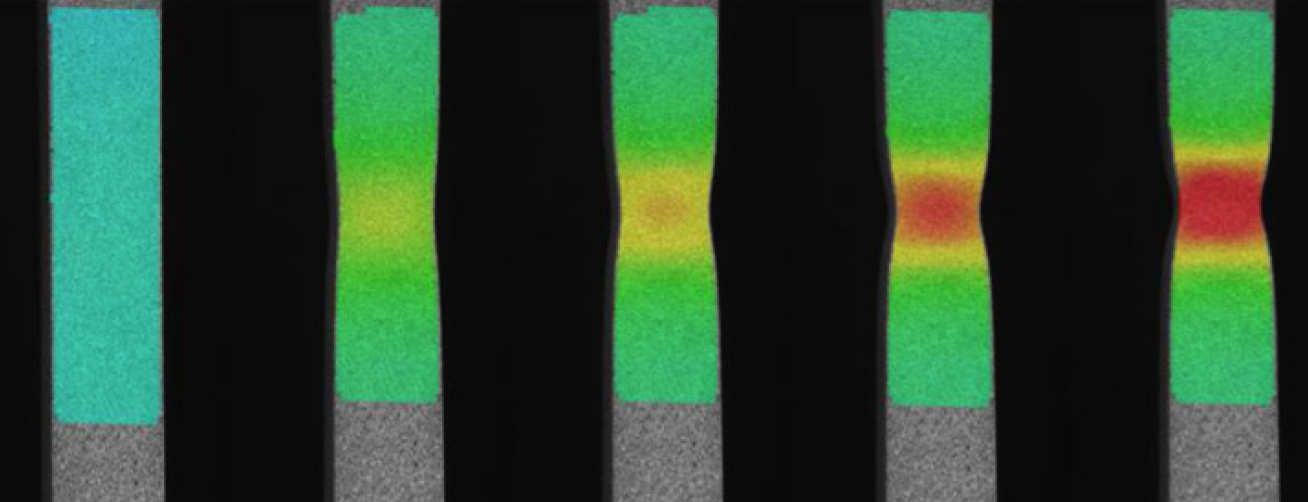

Mei-Chin Pang, Gregory Offer, Mu Chen, John Dear
The most feasible way to achieve clean, efficient and sustainable development in the automotive and aviation sectors, in the long run, is the electrification of the powertrain. In the automotive industry, studies have shown that electric vehicles show promising growth to replace conventional internal combustion engines vehicles in the future progressively. The future development of electric vehicles relies on the advancement of battery technologies. Depending on the type of electric vehicles, the batteries are required to achieve high power or high energy capacity within a given space and weight and at a reasonable cost. Apart from meeting the performance requirements, rigorous safety control is also required for the batteries to operate and respond to a wide range of demanding circumstances such as extreme ambient temperature environment, charge and discharge failures as well as physical damage in crash scenarios. A paradigm shift from conventional lithium battery based on liquid electrolyte to solid-state lithium battery has the potential to mitigate safety concerns such as explosion due to thermal runaway. This project focuses on the modelling of solid-state lithium batteries.
Figure 1 (left) shows the preliminary simulation result of the mechanical model of a thin-film solid-state lithium-ion battery under bending. Figure 1 (right) illustrates that the mechanical model comprises of four layers: a ceramic substrate, a LiCoO2 positive electrode, a Lipon solid electrolyte and a Li negative electrode.
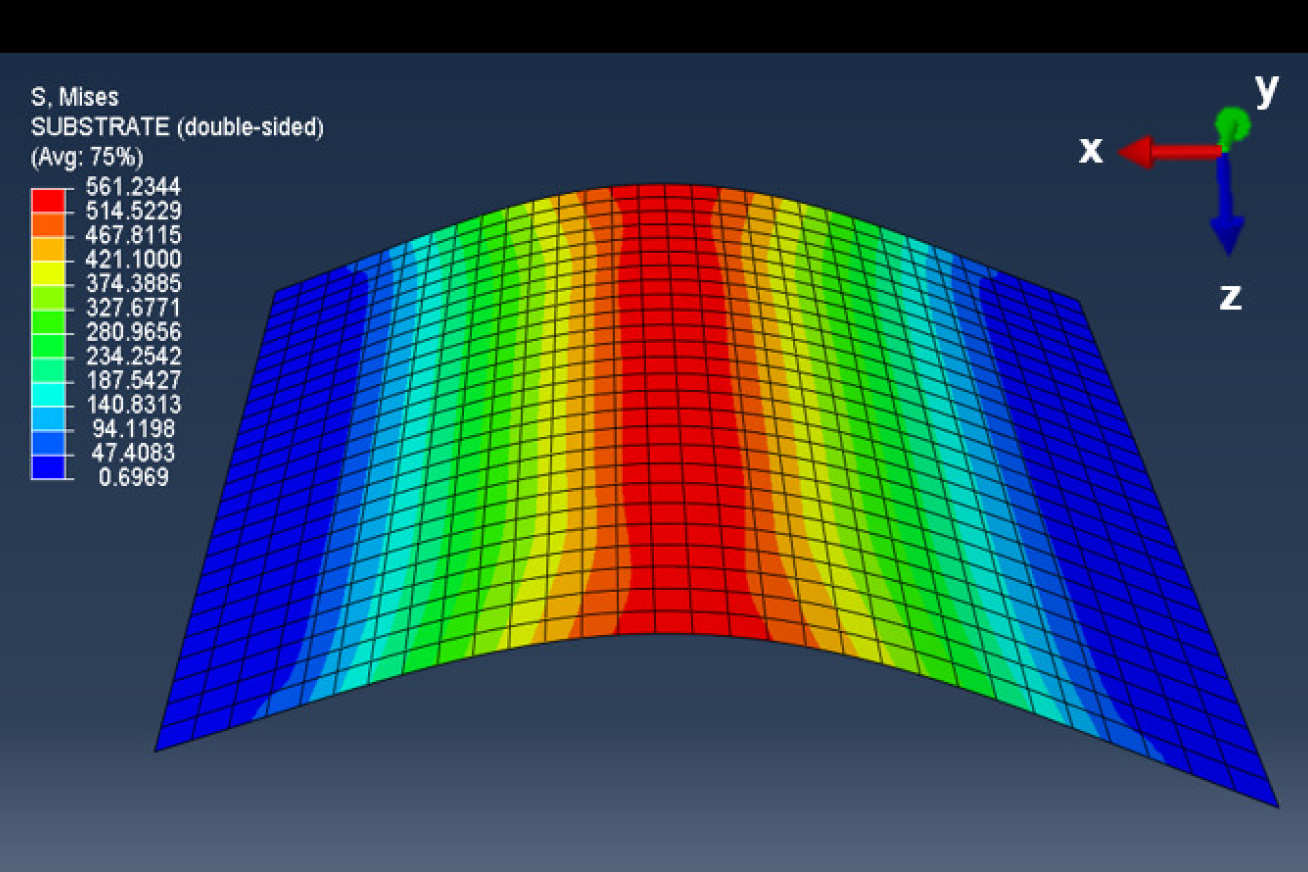
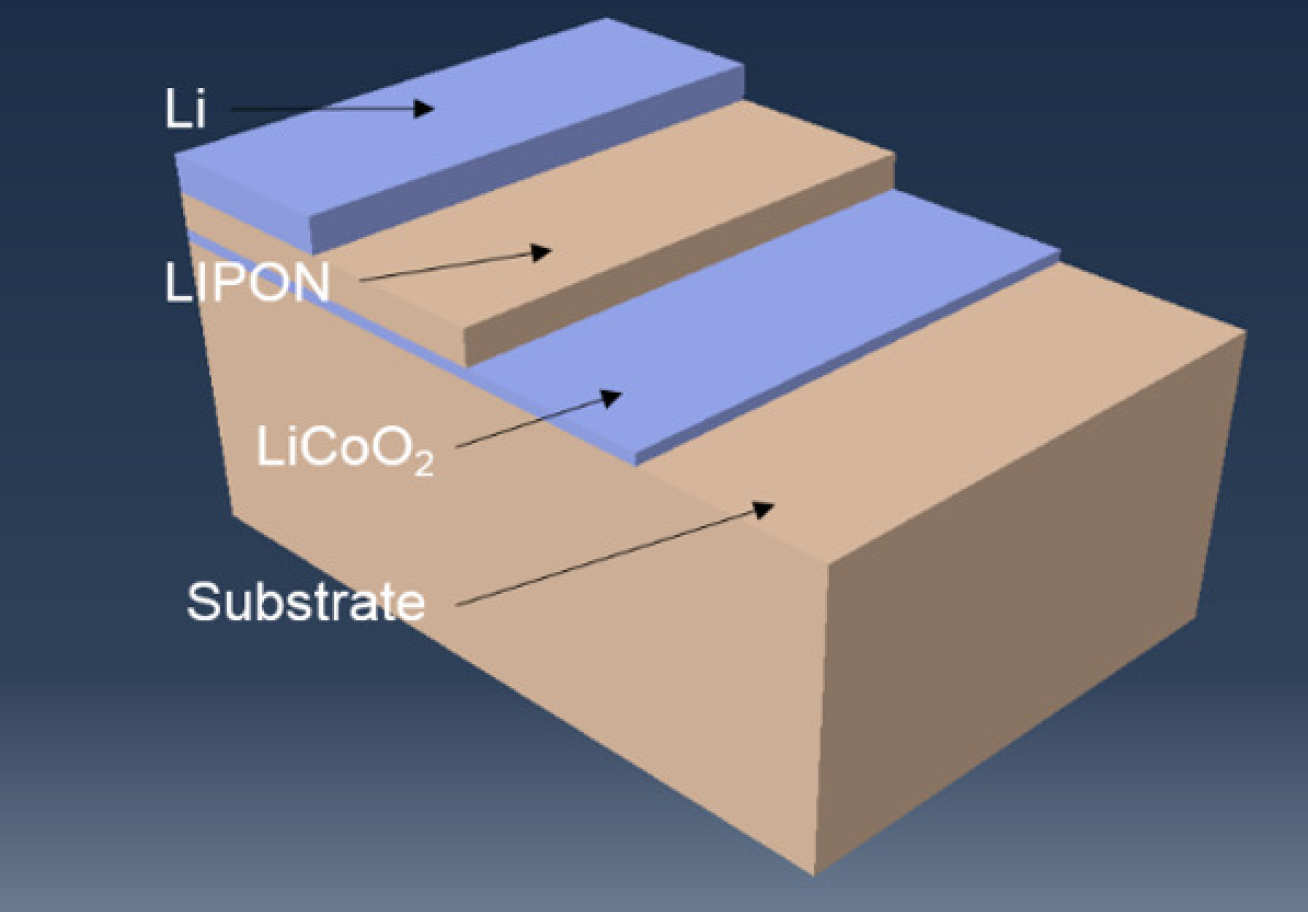
Yan Zhao, Gregory Offer, Yatish Patel and John Dear
There is an urgent need from the automotive and aviation industries to be able to predict the performance of lithium ion batteries and diagnose problems under extremes of operation and realistic conditions. Currently many systems are used outside of normally studied conditions which at best result in poor performance or over-engineered solutions, and at worst failure. This project will meet this need by developing the scientific tools & techniques that are needed by industry to be able to design safe and affordable products around these technologies. This project will therefore develop operational models that include degradation & failure that are capable of performing at extremes of operation, both very high charge/discharge rates and low and high temperatures.
- Extend and improve models for predicting the onset and consequences of thermal runaway reactions in lithium ion batteries, particularly to include the lithiation state of both the anode and cathode
- To extend the normal SEI growth model to overlap with the mechanisms governing extreme SEI layer growth at very high temperatures, essentially to achieve a seamless SEI model that can operate across the full temperature range, including the extremes
- To develop a cathode decomposition model
- To conduct the experiments necessary to parameterise and validate the models, these will involve testing cells to failure
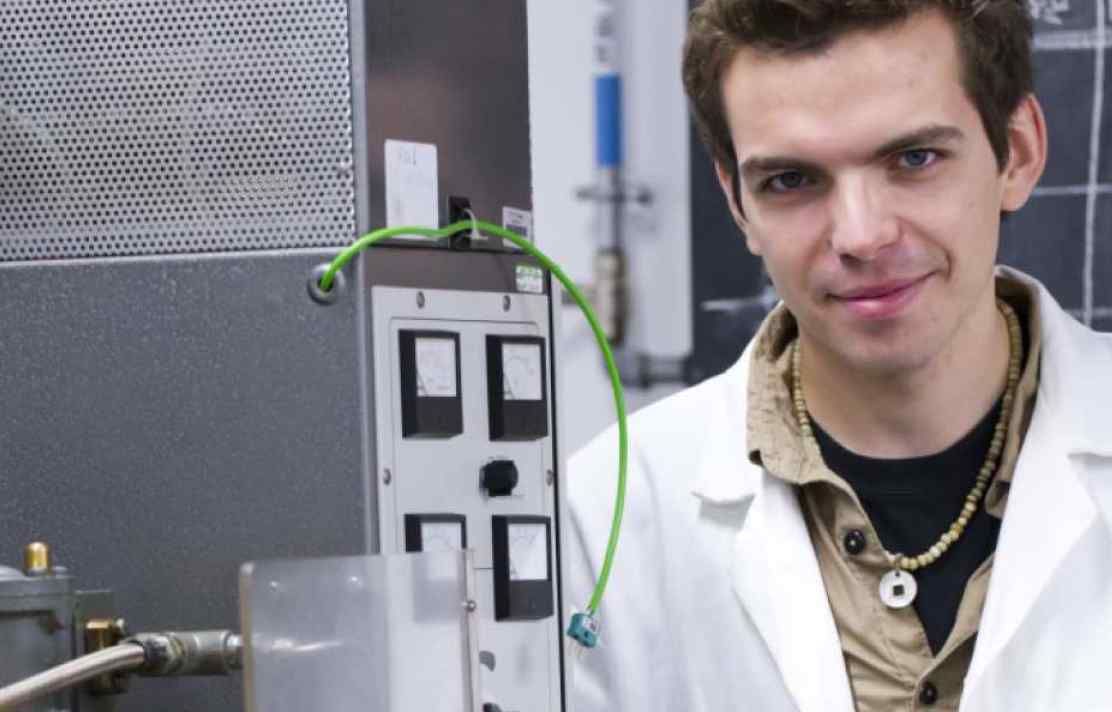
PhD study
Early Career Research Fellowships
Find out more about applying for early career fellowships in our department