Projects
- The adhesive bonding of CFRP to titanium alloy
- The durability of asphalt mixtures
- Improving the mechanical properties of composite-metal joints by Surfi-Sculpt
- Damage tolerance of transparent laminate joints in aircraft applications
- Developing a test method to measure the environmental stress cracking (ESC) resistance of polymers.
Rodolfo Rito, Milad Toolabi, Christoph Schwingshackl, Bamber Blackman
This project is investigating the high cycle fatigue loading of titanium alloy protection strips bonded to a CFRP core. The application is the fan blade of an aero engine where resonances can impose significant vibratory stresses to the structure. The aim is to combine fracture mechanics with FEA modelling to predict the service life of such structures. Experimental results from fracture coupon tests and high frequency structural tests on a shaker facility in the vibrations laboratory being carried out.
Yusuke Kajihara (Academic visitor from University of Tokyo), Ambrose Taylor, Bamber Blackman
In this project the adhesion between aggregate stones and bitumen (here the adhesive) is being investigated with the goal of allowing more durable road surfaces to be constructed. It is well known that asphalt road surfaces break up in winter due to moisture penetration and then the freeze-thaw cycle. An adhesion test has been developed to measure the fracture resistance of the stone-bitumen joint such that the effectiveness of adhesion promoters can be assessed and the mechanisms of failure can be more fully understood.
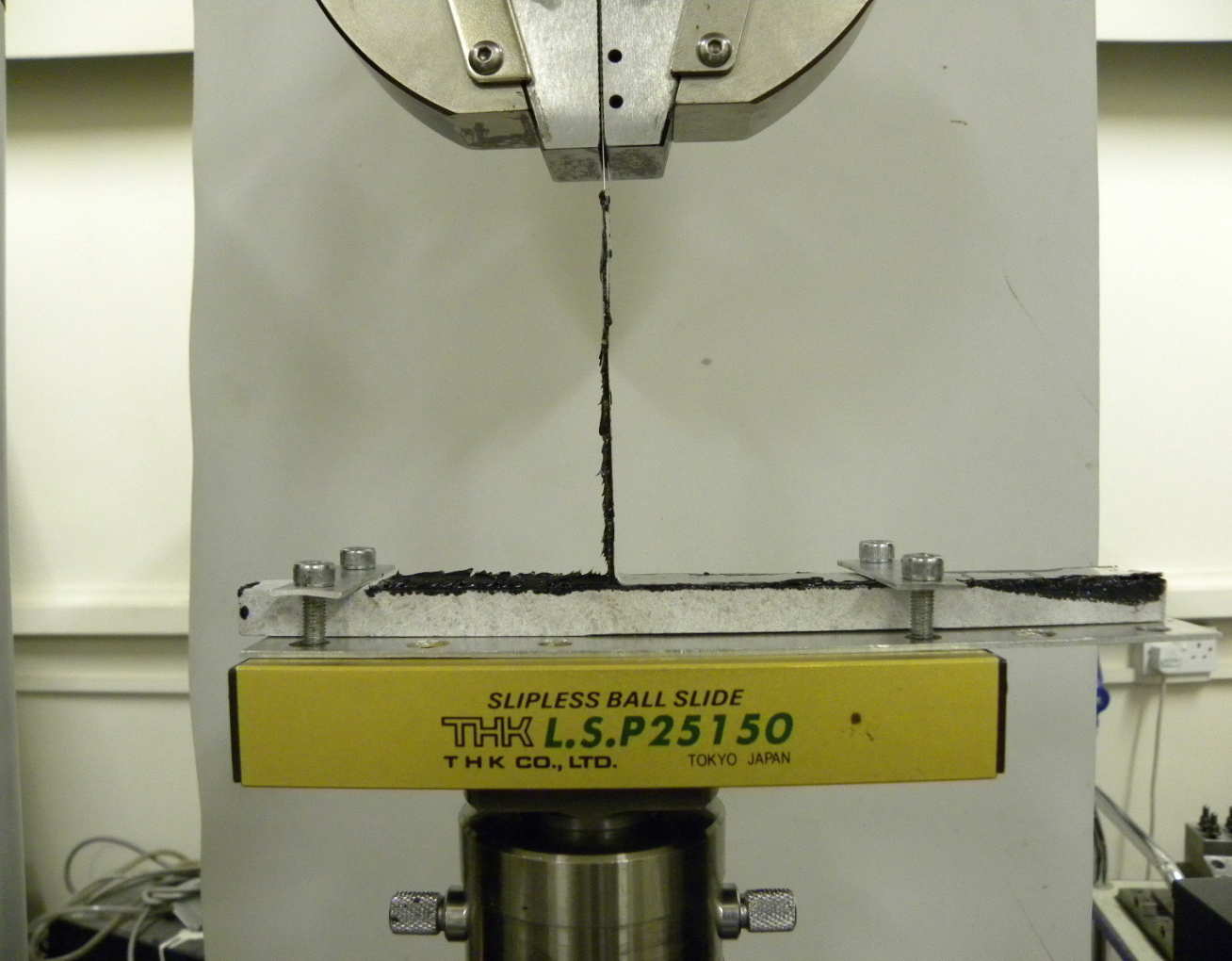

Wei Xiong (PhD student), John Dear, Bamber Blackman
Joining dissimilar material such as carbon fibre reinforced plastic (CFRP) to metals effectively has been a significant challenge. In this project, an innovative joining technology known as Surfi-Sculpt adopts the idea of z-pinning technology in a composite-composite joint by creating arrays of macro-scale surfi-sculpts on the surface of metal part to be joined. With careful joint design, high performance can be achieved in respect of damage tolerance and energy absorption. In this project, the effects of composite lay-up and pin density are being investigated.

Sze Ki (Christine) Ng, (PhD student); John Dear, Bamber Blackman
This project investigates the toughness and damage tolerance of transparent polymers as used in the aircraft industry for cockpit canopies. Such materials will experience a combination of continuous and alternating stresses during their service life, and due to the methods of attaching them to the rest of the structure, will be subjected to stress concentrations at attachment points.
This project will consider the quasi-static toughness, and fatigue of the polymer used, which is a bi-axially oriented PMMA. Fracture mechanics and damage mechanics methods will be employed to understand the in-service behaviour and predict performance.
The fracture mechanics compact tension specimen shown which can be loaded in fatigue at a predefined frequency. This is to simulate repeated pressurised cycles in a cockpit application. In such a test, the rate of crack growth per cycle, da/dN is measured as a function of applied ΔK.
Muhammad Kamaludin (PhD student); Yatish Patel; Gordon Williams and Bamber Blackman
Environmental stress cracking (ESC) is known to affect certain thermoplastics and occurs under simultaneous exposure to both applied stress and a hostile environment. The combination of these can cause a crack to form from a flaw in the material; upon reaching a critical size, the crack may accelerate thus causing catastrophic failure in the component. Various tests have been utilised to measure the resistance of different polymers to ESC, but these are often material- and application-specific and overlook the different stages of the failure process. In this project, a fracture mechanics approach is being developed and applied, with a view to developing a test method that has wide applicability and provides both insight into the failure mechanisms as well as information for engineering design.

Contact us
Professor Anthony Kinloch
Email: a.kinloch@imperial.ac.uk
Tel: +44 (0)20 7594 7081
Website
343 City and Guilds Building,
South Kensington Campus.