Researchers constructing world’s largest 3D-printed bridge reach milestone
Researchers working on the world’s largest 3D-printed steel bridge celebrate another landmark.
Since last summer researchers from The Alan Turing Institute-Lloyd’s Register Foundation programme in data-centric engineering have collaborated with Imperial College London and MX3D, an Amsterdam-based start-up, on plans to design, build and install the world’s largest 3D printed structure – a 12 metre-long bridge – across a canal in Amsterdam.
A crucial next step in the project will be developing the sensor network which enables engineers to measure the bridge’s health in real time and monitor how it changes over its lifespan Professor Mark Girolami Department of Mathematics
The project recently reached a major milestone with the 3D robotically printed span of the bridge complete and revealed to the public.
The Turing Institute brings together a team of structural engineers, mathematicians, computer scientists and statisticians to undertake this innovative project. Scientists from the Steel Structures Research Group at Imperial are leading the research to undertake structural testing on the 3D printed steel, building a vast sensor network on the bridge to monitor its health both during the preliminary tests, and after its final placement.
Professor Mark Girolami, from Imperial’s Department of Mathematics and Director of the Turing-Lloyd’s Register Foundation Programme for Data-Centric Engineering, said:
“This project represents a world-first in engineering and we are delighted to play a role in ensuring the bridge’s success. This recent load testing undertaken by the team at Imperial is a major milestone for celebration.
“A crucial next step in the project will be developing the sensor network which enables engineers to measure the bridge’s health in real time and monitor how it changes over its lifespan.
“This ‘digital twin’ of the bridge will ensure it remains safe to cross in all conditions, and will provide valuable insights to inform designs for future 3D printed metallic structures.”
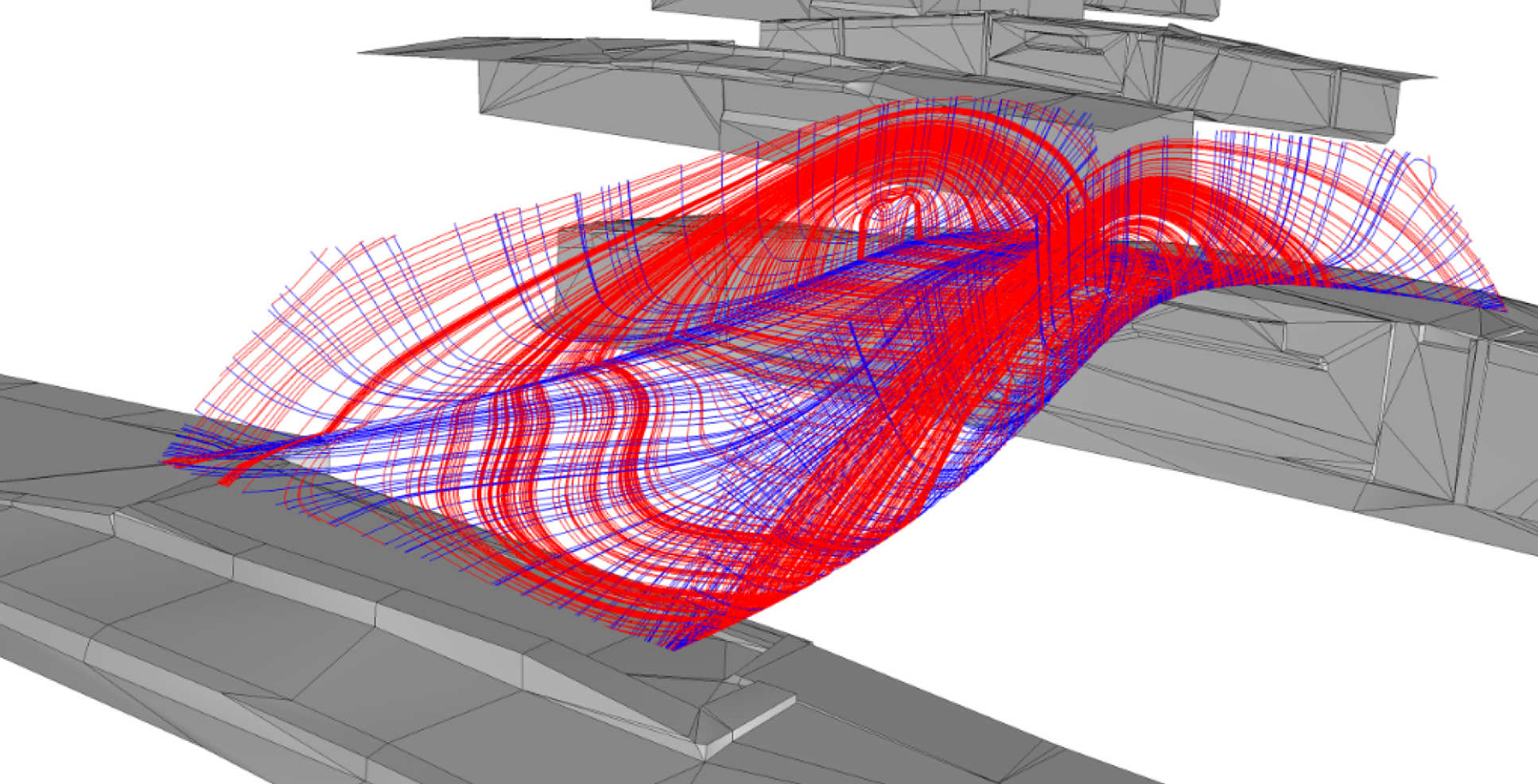
Professor Leroy Gardner, from the Department of Civil and Environmental Engineering, commented on the team’s recent successful testing:
“In the absence of structural design provisions for 3D printed steel, physical testing is an important part of ensuring the safety of the structure. The recent testing confirmed not only that the bridge could withstand the applied load, but also that the numerical simulation of the bridge developed by the Steel Structures Research Group provided an accurate representation of the behaviour observed in practice.”
Group Leader in the data-centric engineering programme Dr Craig Buchanan added: “With the 3D printing of the main structure now complete, we look forward to returning to Amsterdam and proving that the bridge can resist the full design loading it is anticipated to experience when opened to the public in 2019.”
MX3D anticipate that the bridge will be installed before the end of 2019.
Find out more about the project and view images of the bridge being built on the MX3D website.
For more information about data-centric engineering, visit the Turing Institute website.
Find out more about Imperial College’s Steel Structures Research Group.
Article text (excluding photos or graphics) © Imperial College London.
Photos and graphics subject to third party copyright used with permission or © Imperial College London.