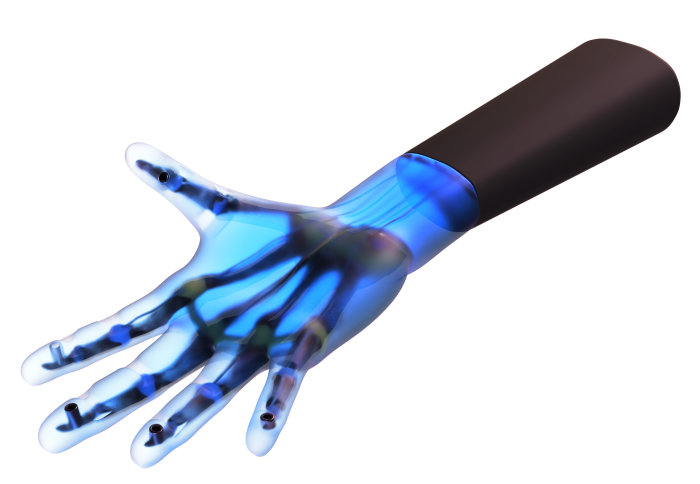
Rendering of a prosthetic hand developed by student, Lois Liow.

Aimed at Year 3/4 MEng Engineering students, the 'Design for Additive Manufacturing' module breaks new ground with its skills-focused syllabus.
Led by Dr Connor Myant and Dr Ajit Panesar, the module takes a subtly different approach to teaching students about additive manufacturing, or as it is more commonly known, '3D printing'.
Dr Myant and Dr Panesar were determined to offer a module that focused less on the technology available right now, and instead provided students with the theory and skills necessary to work in design engineering in the future. A number of industrial partners have been involved in the development of the module and have visited the Dyson School of Design Engineering to speak with students.
"I hope students completing this module leave it with a greater sense of how to 'add value' to their design proposals" Dr Connor Myant
Explaining this focus on the fundamentals of design engineering, Dr Myant said: "Understandably many students, and even staff, are keen to try out a range of new technologies as soon as they become available, however all the industry trends point to the fact that our students are graduating into a world in which there is no one-size-fits-all approach.
"I hope students completing this module leave it with a greater sense of how to 'add value' to their design proposals - is 3D printing the right route or are there are associated technologies that could prove more economically viable or could curb the amount of problems encountered?"
Dr Myant and Dr Panesar's module proposal was created at the same time as the College developed its ambitious Learning & Teaching Strategy. Across the entirety of Imperial Departments and Faculties are taking a fresh approach to the way they teach their students by offering authentic learning experiences. Learning opportunities such as those in the Dyson School are a key part of preparing students for a life after university.
Developing prototypes
Student Lois Liow developed ERYX, a conceptual anthropomorphic robotic prosthetic hand with varying material stiffness. The hand is made in the image of a real human hand - with rigid bones, flexible ligaments and compliant skin to replicate its feel.
The multi-material design allows the hand to be fabricated as a single print, removing any need for assembly that would otherwise be needed for conventional robotic prostheses.
"One of the most challenging tasks facing engineers is having to select the best-suited technology for a specific design or application. Not only does the module cover this, but it also teaches how to optimise and adapt the design for greater benefits." Lois Liow MEng student
Lois said: "There has been a lot of hype around 3D printing recently and having used a range of printers before, I thought the module would be an interesting experience.
"One of the most challenging tasks facing engineers is having to select the best-suited technology for a specific design or application. Not only does the module cover this, but it also teaches how to optimise and adapt the design for greater benefits, which may not be possible with traditional manufacturing methods."
Lois has been prototyping with 3D printers for a number of years, but has never had the opportunity to learn the theory and mechanisms behind different 3D printing technologies.
Lois said: "With previous experience as a mechanical engineering intern, I can say with confidence that designing for additive manufacturing is a much needed skill in the industrial R&D sector. This module has given me a better understanding of the processes behind each method of 3D printing and their limitations."
Putting theory into practice
Andrew Triantaphyllou of the Manufacturing Technology Centre, has been involved at various stages of the development of the module.
Andrew said: "Our industrial members have highlighted knowledge in additive manufacture as an important requirement for the next generation of UK engineers. It is vital that they know about this rapidly evolving technology, and are trained in the new design processes required for it’s optimal use.
"I was happy to provide an industrial view-point to Dr Myant when forming the blueprint for his module. It is great to see that Imperial College understand the importance of partnering with industry to insure that industry’s interests are covered.”
Steven Parkinson of the design software company Autodesk, has also been involved in the development of the module.
"Additive manufacturing is set to be a major UK industry sector in the near future. It is vital that the next generation of engineers have the skills and knowledge to unleash this technology to its true potential." Steven Parkinson Autodesk
Steven said: “Additive manufacturing is set to be a major UK industry sector in the near future. It is vital that the next generation of engineers have the skills and knowledge to unleash this technology to its true potential. Additive manufacturing can open new design spaces previously unavailable in traditional manufacturing.
"However, to do this engineers need to push design software beyond traditional technical drawings into advanced 3D modelling and computational techniques; such as optimisation and generative methodologies, complex geometric forms and automated design processes.
"At Autodesk we are developing the next generation in design and manufacturing platforms ready for the 3D printing revolution; so we are proud to support this module, and the work Dr Myant and Dr Panesar are doing."
Article text (excluding photos or graphics) © Imperial College London.
Photos and graphics subject to third party copyright used with permission or © Imperial College London.
Reporter

Murray MacKay
Communications Division