

Hamlyn researchers proposed a novel functional atraumatic self-shaping cochlear implant, aiming to aid patients suffering from hearing loss.
Cochlear implants (CIs) have been shown to improve hearing in patients suffering from sensorineural hearing loss.
CIs bypass the function of the damaged ear by converting sound into electrical pulses. CIs deliver electrical pulses to the hearing nerve via an electrode array (EA) that is carefully inserted in the scala tympani in a complex surgical procedure.
However, current CIs can cause trauma during insertion, threatening hearing preservation. Thus, existing pre-curved CIs use external mechanisms to be inserted.
A Novel Functional Atraumatic Self-Shaping Cochlear Implant
To overcome the obstacles current CIs might cause during surgery, our researchers at the Hamlyn Centre proposed a novel functional atraumatic self-shaping cochlear implant. It is a pre-curved CI that curls into the cochlea under the influence of body temperature.
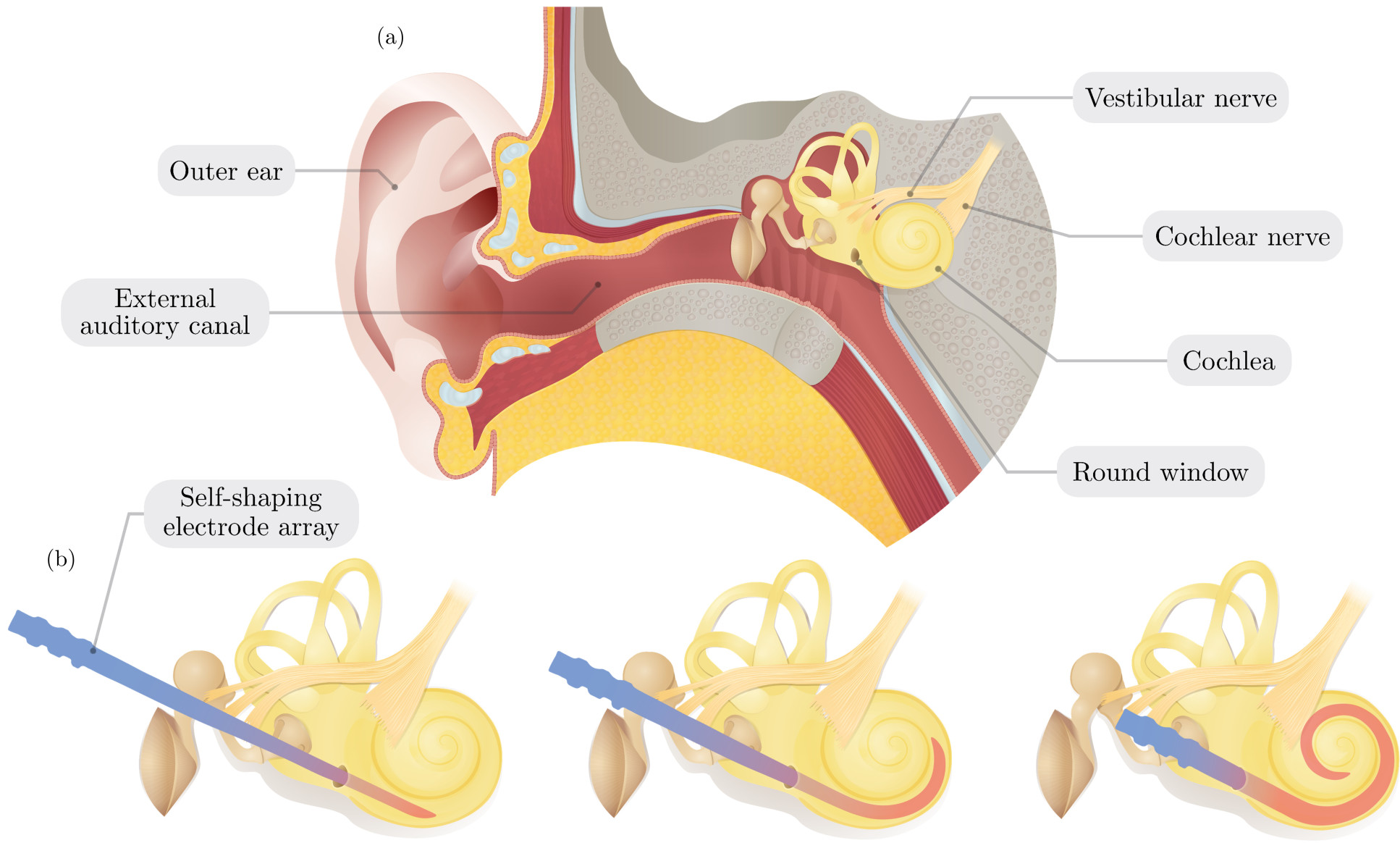
By comparison to existing CIs, the proposed device can be smaller and easily inserted. The implant material is implemented in COMSOL to simulate its behaviour, and an analytical study is conducted to verify the material model.
Moreover, two additional studies are carried out to assess the implant recovery forces and their ability to recover shape even with embedded metal.
Numerical modelling and experimental tests suggest that the CI recovery forces are below the rupture threshold. The recovery study in a functional self-shaping CI shows that the device will still be able to curl in the cochlea.
This implant concept has thus shown potential to be eventually used in clinical practice and improve hearing outcomes seen at present.
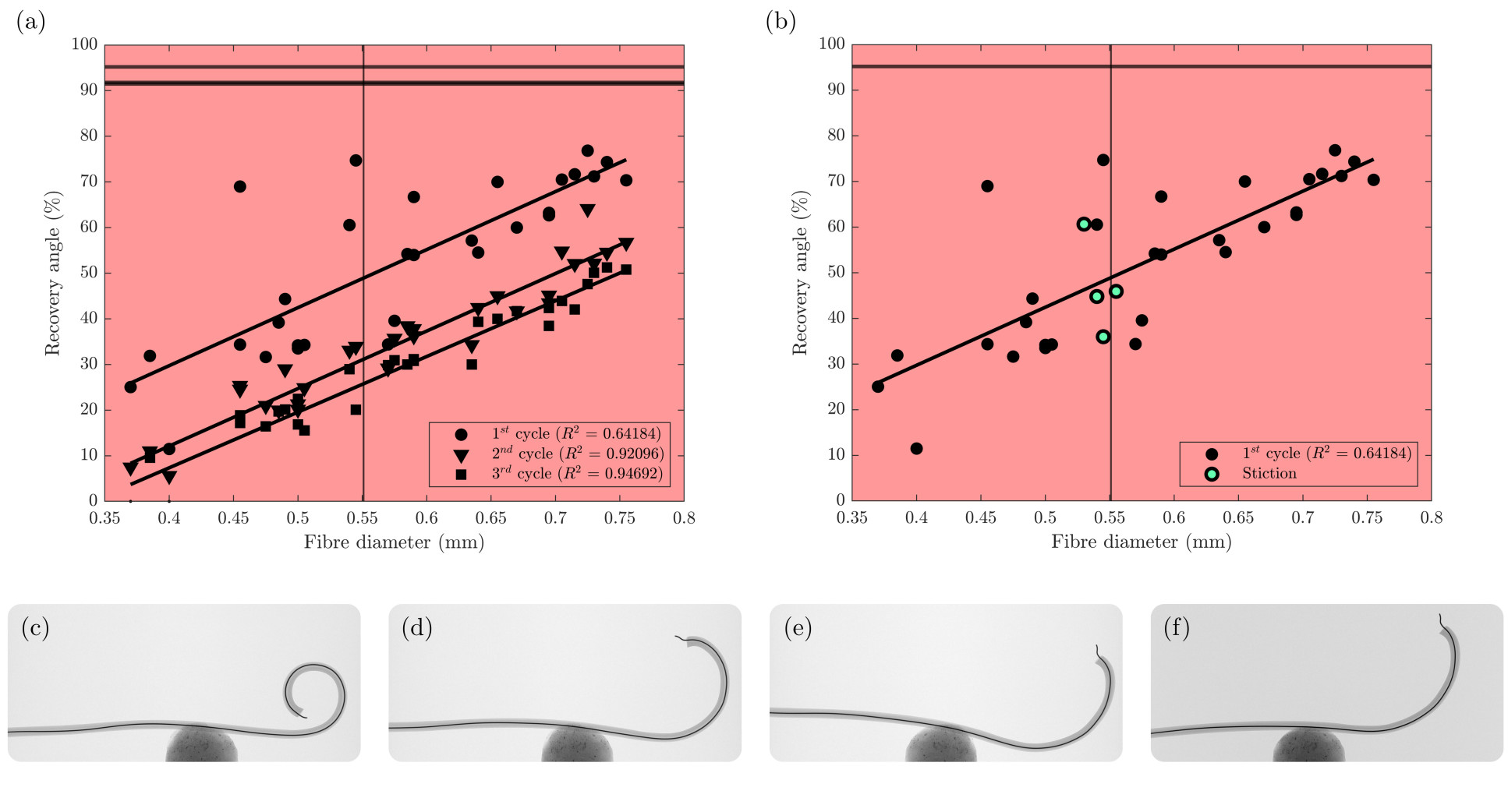
This research was supported by EPSRC Programme Grant “Micro-robotics for Surgery (EP/P012779/1)” (Daniel Bautista-Salinas, Mohamed E. M. K. Abdelaziz, Burak Temelkuran, Eric M. Yeatman, Charlie T. Huins, and Ferdinando Rodriguez y Baena, "Towards a Functional Atraumatic Self-Shaping Cochlear Implant",Macromolecular Materials and Engineering, October 2021).
Supporters
Article text (excluding photos or graphics) © Imperial College London.
Photos and graphics subject to third party copyright used with permission or © Imperial College London.
Reporters
Daniel Bautista Salinas
Department of Mechanical Engineering

Contact details
Email: d.bautista-salinas18@imperial.ac.uk
Show all stories by this author

Erh-Ya (Asa) Tsui
Enterprise

Contact details
Email: press.office@imperial.ac.uk
Show all stories by this author