Industry consortium to develop modern chemical manufacturing methods


A major consortium led by Imperial and chemical company BASF is to help make chemical manufacturing more efficient, resilient, and sustainable.
Imperial will receive £17.8 million from the Engineering & Physical Sciences Research Council (EPSRC) and industry partners under the EPSRC Prosperity Partnership programme in a consortium of organisations from across the chemicals value chain.
Flow chemistry is inherently more sustainable because it makes better use of heat and materials. It can also provide a powerful tool for automating production and the research and development of more sustainable processes. Professor Mimi Hii
The partnership on Innovative Continuous Manufacturing of Industrial Chemicals (IConIC) is led by BASF and also includes Almac, AM Technology, CPI, METTLER TOLEDO Autochem, Siemens Process Systems Engineering and Sterling Pharma Solutions, who will pool their expertise to advance flow chemistry, a production technique in which the required reactions take place in continuous operation rather than in batches.
Like the introduction of assembly lines to car manufacturing at the turn of the 20th century, flow chemistry allows manufacturers to produce more consistent products, use energy and materials more efficiently, and introduce greater automation.
“Flow chemistry is inherently more sustainable than batch processing because it makes better use of heat and materials,” said lead investigator Professor Mimi Hii from Imperial’s Department of Chemistry. “It can also provide a powerful tool for automating production and the research and development of more sustainable processes. However, there are technical bottlenecks that are holding back its full implementation. Through this new consortium we will be in a strong position to address these.”
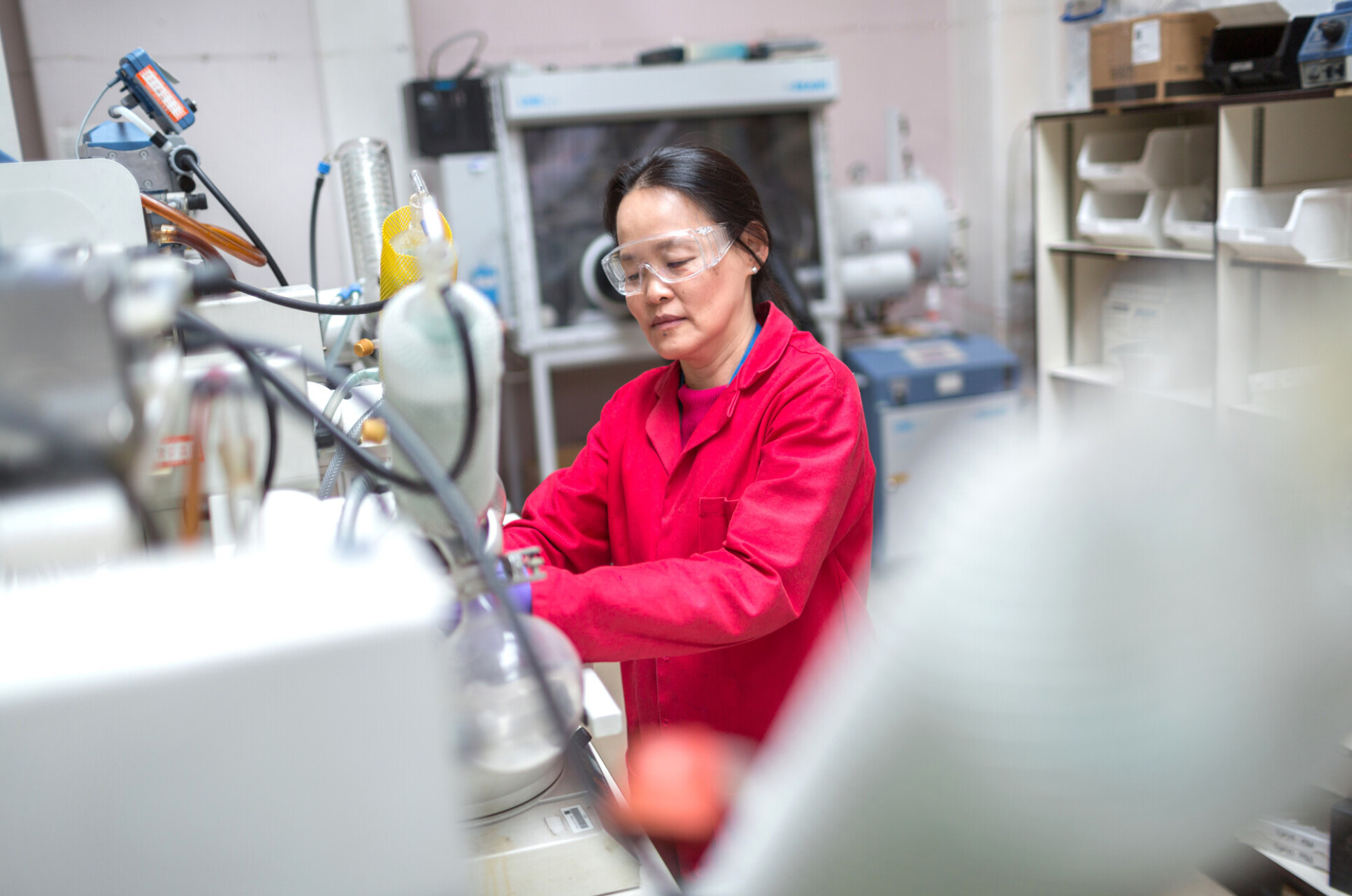
Major partnership
Professor Ian Walmsley, Provost of Imperial, said: “We’re delighted to have brought together this outstanding consortium. By combining the sector-specific knowledge of leading industrial innovators from across the chemical value chain with Imperial’s world-leading research capabilities in chemistry, engineering, and computing, the partnership will help create important advances in industrial chemistry. In turn it will support the UK government’s industrial strategy and help create a more productive, resilient, and sustainable chemical sector.”
Dr Helmut Winterling, Senior Vice President for Digitalization, Automation and Innovation Management, Group Research at BASF, added: “Building on our long track-record in collaborating with leading data-scientists at Imperial, we will also advance the development of products and processes in the chemical industry by optimally combining experimental and digital capabilities toward an integrated workflow. This workflow within IConIC highlights the interdisciplinary and holistic approach that is at the heart of our strategic partnership.”
Industry step change
By making more advanced and efficient manufacturing methods available even at smaller production facilities, we aim to make the chemical industries more resilient to the supply chain shocks and increases in energy and material costs we’re becoming increasingly familiar with. Dr Darren Budd BASF
The research will aim to help the chemical industry respond to a range of pressing challenges. Dr Christian Holtze, Principal Scientist Flow Chemistry at BASF, said: “From an industry point of view, we’re facing three major challenges that could mark a step change from the way the chemical industry has developed over the last 150 years: With climate change, industrial societies are striving for net zero. During the pandemic, we learned that our supply chains need to be more resilient. And the shortage of natural gas has clearly demonstrated our need for alternative feedstocks. To tackle these challenges, we will need to innovate novel production processes for future value chains in the chemical industry.”
The partners will carry out research spanning chemistry, engineering, and advanced data science to generate the know-how and intellectual property required to make continuous processing work effectively at smaller scales, including in research and development labs, pilot facilities, and in the production of high-value chemicals such as pharmaceuticals, agrochemicals, and speciality chemicals.
“By making more advanced and efficient manufacturing methods available even at smaller production facilities, we aim to make the chemical industries more resilient to the supply chain shocks and increases in energy and material costs we’re becoming increasingly familiar with,” said Dr Darren Budd, Commercial Director at BASF UK and Ireland and an IConIC principal investigator.
Clean growth
The research will support the ‘Artificial Intelligence and Data’ and ‘Clean Growth’ challenges in the UK’s Industrial Strategy, and has potential to benefit the UK economy by helping create new high-skilled employment opportunities and investment into Scotland and the Northern Powerhouse regions. These regions already produce many of the world’s industrial chemicals but lack the large-scale ‘Verbund’ sites employed by companies like BASF in countries such as Germany and China.
The announcement also marks a significant new phase in Imperial’s strategic partnership with BASF, which it signed a master research agreement with last year. With a new cohort of postdoctoral researchers and industry partners from across the supply chain on board, the project team will adopt a holistic approach that will help accelerate innovation in the sector.
The consortium is aligned with Imperial Zero Pollution, a major College-wide initiative that aims to help create the societal and industrial systems needed to transition to zero carbon and other forms of pollution.
Innovation ecosystem
The consortium will benefit from the scientific expertise of three world-leading academic departments at Imperial and the College’s advanced infrastructure including automated chemistry facilities ROAR, ATLAS, and DigiFAB, the AI centre I-X, and the prototyping community Advanced Hackspace.
These facilities are located in the White City Innovation District, an emerging West London centre for deep science and innovation that brings together startups, major businesses, and academic researchers.
UKRI Centres for Doctoral Training (CDTs) including the CDT in Next Generation Synthesis & Reaction Technology (rEact) and another in Modern Statistics and Statistical Machine Learning (StatML) will support the training of a new generation of researchers skilled in advanced manufacturing.
Consortium partners will benefit not only from access to new technologies developed by IConIC, but access to the White City ecosystem and the opportunity to work with talented research students who could provide the skills needed to create a rejuvenated green chemical industry.
Photo at top: BASF SE
Article text (excluding photos or graphics) © Imperial College London.
Photos and graphics subject to third party copyright used with permission or © Imperial College London.